Sharded Thread (7/8)
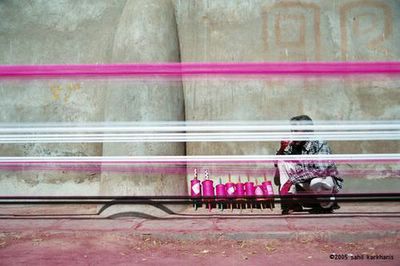
After all the hard work, a well deserved rest... I`ll sit on my haunches and sip tea...
_____
Nikon F75, 28-110mm
Fuji 100 ISO
2005, Ahmedabad, India
Sharded Thread (6/8)
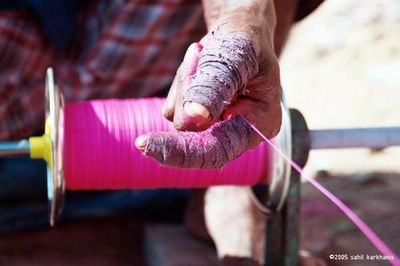
Spooling it all in... All that pristine-white yarn transformed by dint of hard work into fuschia coloured glass-shard coated lethal `manja` needs to be spooled on to wooden, metal or, increasingly nowadays, tacky-plastic `firkis` before it can be sold... The colourful firkis serve as point-of-purchase and product rolled into one... It`s a sight to see, all that colour by the roadside...
But these rag-covered, cut and bruised hands tell the real story behind the `manja`... And tell it only too well, I think...
_____
Nikon F75, 28-110mm
Fuji 100 ISO
2005, Ahmedabad, India
Sharded Thread (5/8)
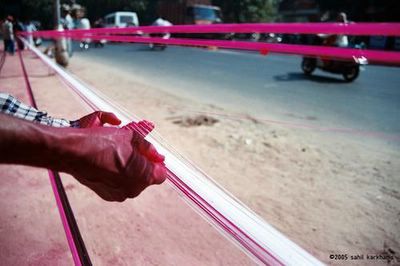
The process of dyeing the yards and yards of stretched out yarn is probably the most demanding. Coloured dye, organic glue (usually made from rice water) and glass shards are all mixed together as a paste. The bright fuschia colour is ample warning to everyone that handling the material can be potentially dangerous; the glass shards are lethal!
These pair of hands shown here have been hardened through weeks of handling the lethal paste. These people are usually too poor to afford protective gloves or suchlike. Some of them do have rags of old cloth wrapped around their `dyeing` hand to afford some protection, but most of them just live with the cuts and bruises as professional hazards...
_____
Nikon F75, 28-110mm
Fuji 100 ISO
2005, Ahmedabad, India
Sharded Thread (4/8)
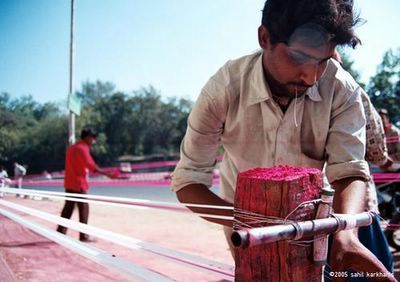
It never ceases to amaze me how surprisingly organised even some of the more unorganised sectors of the industry can be; with clearly defined heirarchy and job profile!
This man, for instance, supervises the entire yarn-stretching process. After the young kid is done walking between the posts laying out the yarn, it`s upto this man to ensure it`s been done right; that the threads are evenly spaced out on the holdfasts and that the yarn is neither too taut or too slack. Only when he`s completely satisfied does the actual dyeing process begin!
_____
Nikon F75, 28-110mm
Fuji 100 ISO
2005, Ahmedabad, India
Sharded Thread (3/8)

Stretching yarn might seem like childs play, but this young lad walks close to 10 kilometers on an average working day stretching the white yarn between the two wooden posts. He works from seven in the morning till about sundown and earns about Rs.50 (a little over a dollar) for all that...
_____
Nikon F75, 28-110mm
Fuji 100 ISO
2005, Ahmedabad, India
Sharded Thread (2/8)
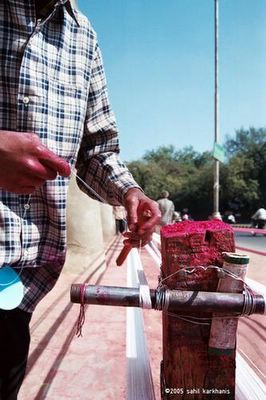
White yarn must first be carefully stretched out, each strand carefully spaced away from the other, so that the dyeing is even and fast. Makeshift wooden posts, stuck into the dusty roadside, serve as cheap and efficient fixtures on which to stretch the yarn. Metal pipes, rods, anything long and tubular tied or nailed onto the posts serve as holdfasts so that the yarn doesn`t slip or sag during dyeing.
The gnarled wood adorned with bright coloured powder dye; the worn-smoothnes of the pipes; the twisted wires; the stark white yarn and the well worked hands of the person plying the yarn makes for an interesting combination of textures..!
_____
Nikon F75, 28-110mm
Fuji 100 ISO
2005, Ahmedabad, India
Sharded Thread (1/8)
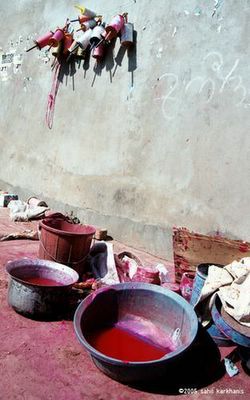
Uttarayan is the festival of kites, celebrated in early January throughout India (under various names, depending on the region) to celebrate the change of season. Winter gives way to spring, the direction of the wind changes and suddenly the sky is awash with kites.
This colourful time of the year is a favourite for photographers who want to capture the ebulient spirit and the joi de vivre of Uttarayan. I have tried it on occasion in the past. The colourful, and fanciful, kites; the blaring music; clear blue skies and pleasant weather; people- old and new alike, wallowing in the fun that`s so intrinsic to the festival. It`s the perfect time of the year. This year, for a change, I thought it would be a good idea to document the saga of the manja- the sharded yarn that`s used to fly the kite, rather than the colourful kites or the mood of the moment.
I`d love to have your comments.
_____
Come Uttarayan and the roadsides are dotted with manja makers. Impromptu roadside set-ups to manufacture manja- the glass shard coated yarn that`s used to fly the kite. The mid-air duels between kite fliers is a sight worth watching with each trying to outfly the other- the winner is the kite that stays flying; the loser, the one with just a cut string in his hand, watching his kite floating away.
Bright coloured dye, glass shards, glue and, of course, yarn. The raw materials that go into making the spools and spools of manja that are consumed during this two day festival.
_____
Nikon F75, 28-110mm
Fuji 100 ISO
2005, Ahmedabad, India
Flirting- In stone | Entry for Moody Monday- Sportive

[Edit]
Entry for Moody Monday
Sportive: Archaic. Amorous or wanton
[/Edit]
______
The step well at Patan, about 130 kilometers north of Ahmedabad, is known as Rani ki Vaav, or `The Queen`s Well`. It consists of a series of steps descending from ground level, in seven tiers, to a natural spring at the bottom.
The historic town of Patan served as the capital of the state of Gujarat for around 600 years, between the 8th and 14th centuries AD, under the Solanki kings. The step well at Patan served as the private bathing pool of Rani Udayamati, the consort of King Bhimadeva, the most illustrious of the Solanki kings.
The walls and pillars, all the way down to the seventh, and lowest, level are adorned with sculptures of gods, godesses and mythological characters from the Hindu pantheon. The coquettish Apsara (or celestial nymph) revelling in her vanity is a recurring motif in a lot of Hindu architecture of that period.
_____
Nikon F75, 28-110mm
Fuji 400 ISO
2004, Patan, North Gujarat, India